RoboRacing has been working on an autonomous go-kart since 2019 and have learned and iterated on every aspect of their vehicle. This is certainly the case with the drive motor system.
When the team first began evGP, a few hardware components were required as part of the rules to be standardized across the robots. Some of those components included a specific Top Kart frame, batteries, and motor component combination. This was originally to give equal footing to new competitors and allowed for the teams to focus on a reduced quantity of components and systems not specified by the rules.
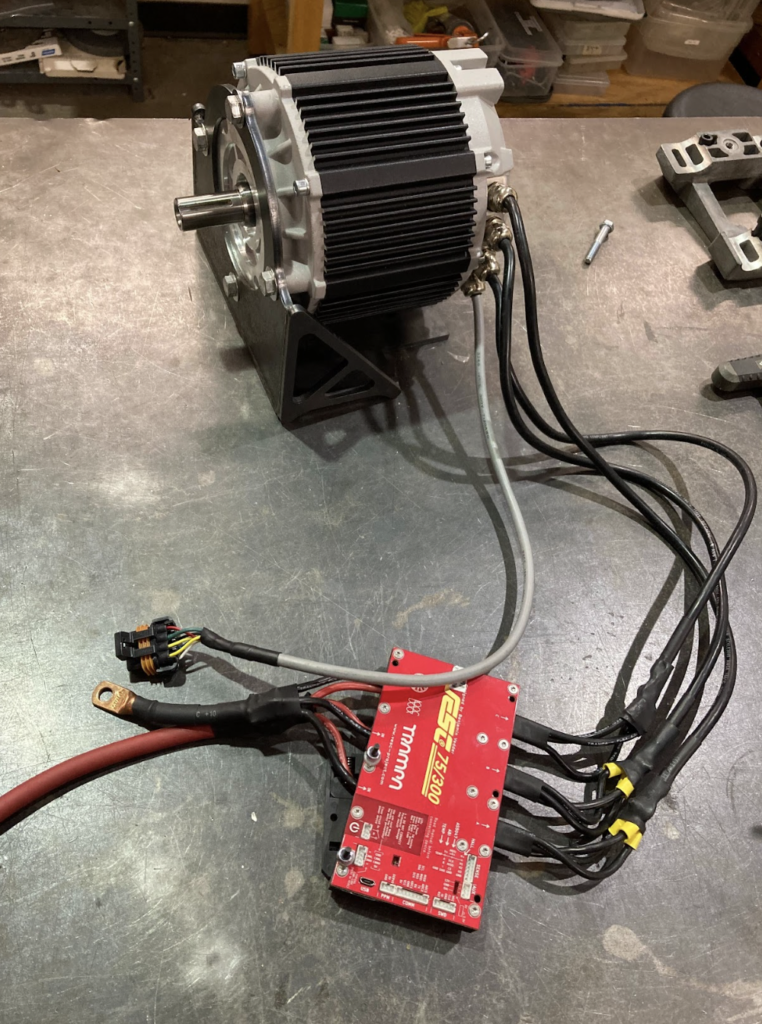
For the drive system, all of the teams were required to use a brushed motor (ME0708) with a golf-cart motor controller (SR48300) and an optional reversing contractor (SW202). Using current sensors, encoders, and practical application of Georgia Tech controls classes, the team was able to compete in two evGP competitions with the drive system. However, there were some control bugs with the golf-cart motor controller. This caused “interesting” events like the robot unexpectedly driving forwards / backwards and low speed control resulting in the car starting and stopping constantly. Additionally, talks in the competition planning had resulted in the expansion of possible drive systems, specifically using brushless motors.
Brushed style motors, as was originally on the robot, were some of the most widely used motors for many years in industrial automation. They were very easy to actuate with only a voltage potential being applied across the two wires and are still very often found in cheap toys because of the simplicity. Brushless motors, in comparison, have three wires that need specific timing to turn on and off in a pattern, with this added complexity limiting adoption in smaller scale / hobbyist applications. Brushless motors have since exploded in popularity and availability due to more efficient energy/weight ratio and longer lifetime compared to brushed motors.
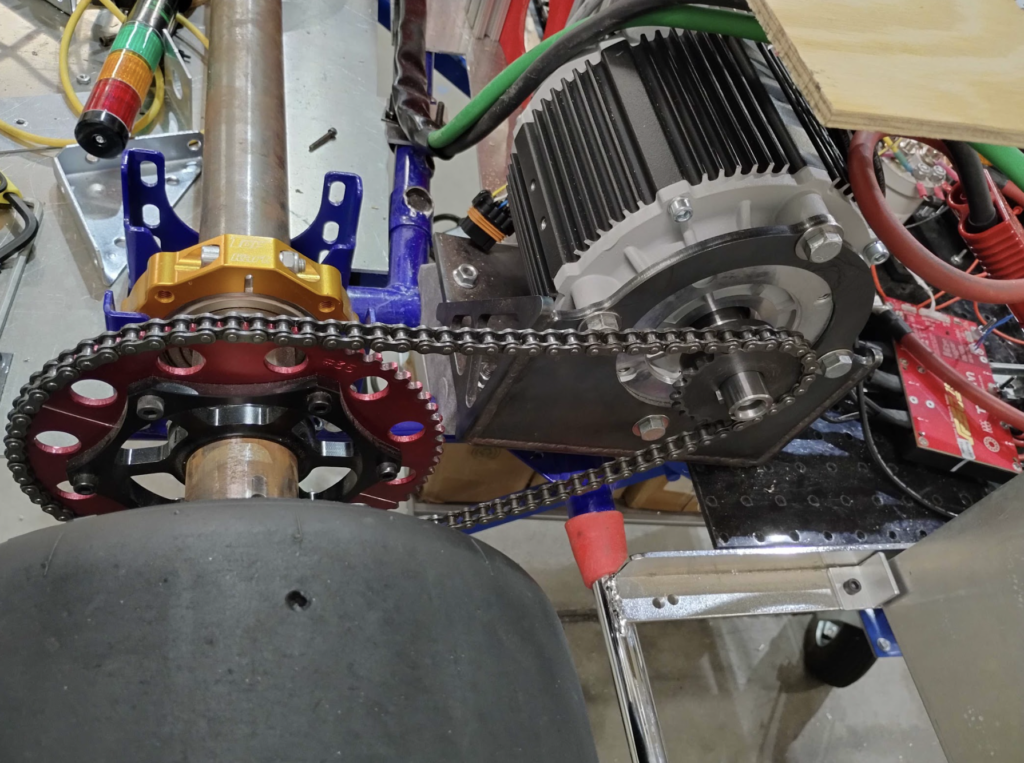
This combination of factors has led the team to switch to a new brushless motor (Golden Motor HPM5000B) and motor controller (VESC 75/300R3) for actuating the drive system. The new VESC controller includes the capabilities to measure current and voltage along with customizable filters, proving much more sophisticated than the original motor controller and allowing for more tightly integrated speed control. The new system also allows for the removal of the reversing contactor, which was heavy and generated lots of heat in the closed enclosure, while maintaining the reversing ability. RPM control has been proven with the motor and controller, with additional development required for full robot drive control.