This past May RoboRacing attended evGrand Prix Autonomous 2022, our second entrance into the competition. The team’s first entrance to this competition was back in mid-September, and only 8 months later Rigatonii (another “i” included) was back on the track at the Purdue Grand Prix Track in Lafayette, Indiana. The team finished 4th place out of 6 overall, making it down the straightaway and around a turn.
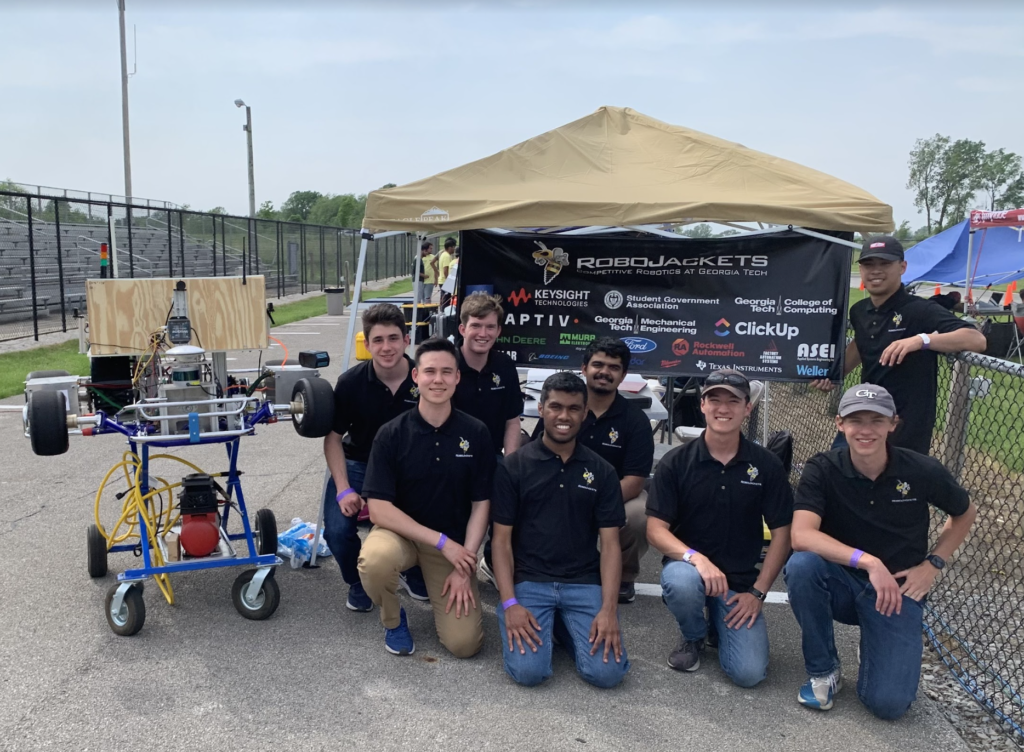
The goal of the competition is to have go-kart scale autonomous head-to-head racing. As the competition is still relatively new and building up to head-to-head racing, the current format is the winner is determined by the fastest time completing 5 laps, increased from 3 laps last year.
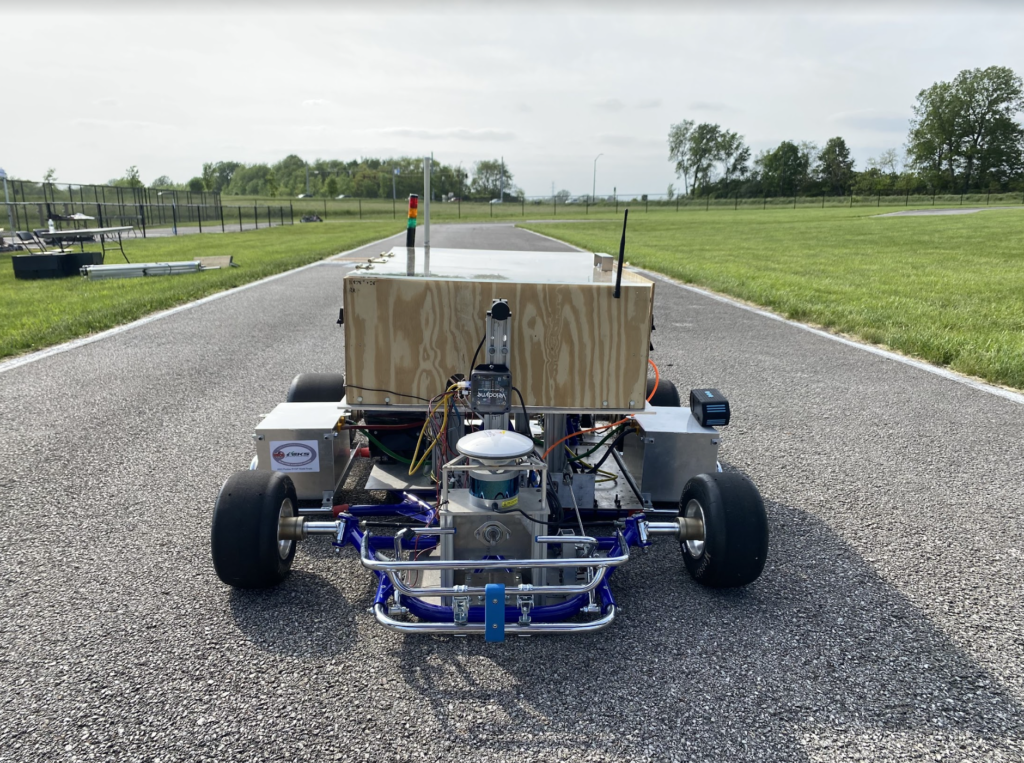
One of the biggest visual changes to the robot was the addition of “The Box”, originally intended to be a large plastic box that contained most of the electronics and cabling. The single container design allowed for the consolidation of at least 3 enclosures and approximately 15lbs in weight saving, being incredibly helpful with general movement of the robot and controls. Additionally, it greatly reduced wiring complexity and allowed the robot to be much easier to waterproof, with racing in light rain a very real possibility at this competition. Unfortunately, due to supply chain related delays, the box had to be made out of wood. This did eliminate the easier waterproofing, but retained other benefits of the centralized electronics enclosure.
At EVGP 2021, the motors used for steering and braking were stepper motors that burnt out due to underestimating the torque required to steer/brake. To correct this problem on the new revision, a mechanism redesign to reduce torque paired with a switch to brushless motors for more power (and torque) helped both the steering and braking theoretically be controlled on the robot. New custom PCBs interfaced with the ODrives, allowing a transition to STM32 for more advanced controls and interfaces. The entire robot was also rewired to take advantage of the single consolidated electronics plate, easing maintenance and improving grounding/signal integrity, from the box addition.
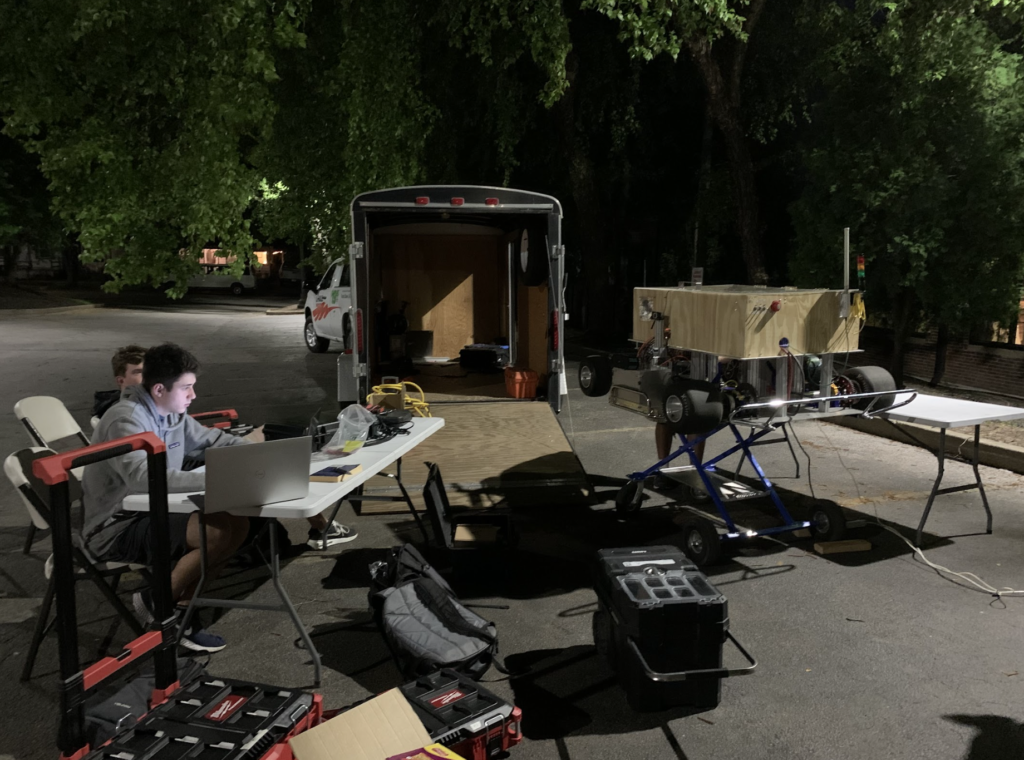
When the team started the week-long competition on Tuesday, some issues were identified with the ODrives, the motor controllers used for controlling both the steering and braking systems. The ODrives, while incredibly customizable, are difficult to debug and can be easily damaged. Debugging and replacing the ODrives consumed many competition days (and nights) of the members in attendance. Once the steering and braking systems were electrically working around Friday, it was unfortunately still understeering compared to what software was commanding, making it very difficult to complete the road course track with both direction turns.
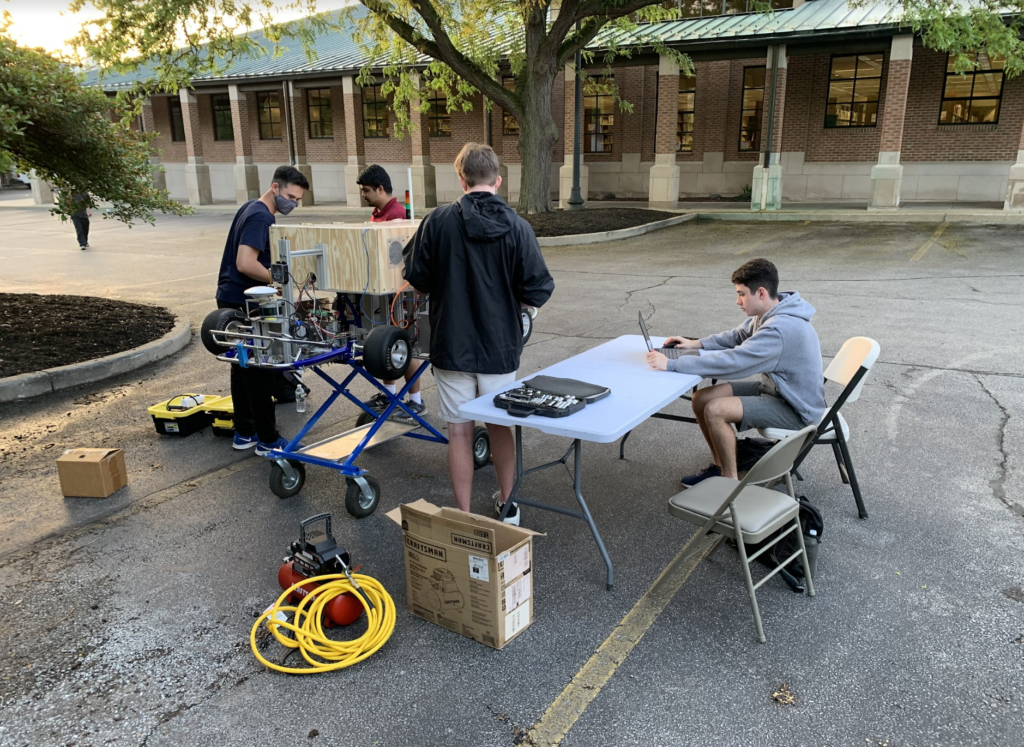
The software team has been transitioning to ROS 2, which includes a brand new high level control planner. This re-write is still in progress, so the existing planner was used at competition. Using the existing planner, paired with the understeering issues, caused some technical performance issues with the robot such as always going in reverse. Additionally, some parts of competition were spent configuring the wireless communications system to work with the track network, an important precursor to multi-robot racing.
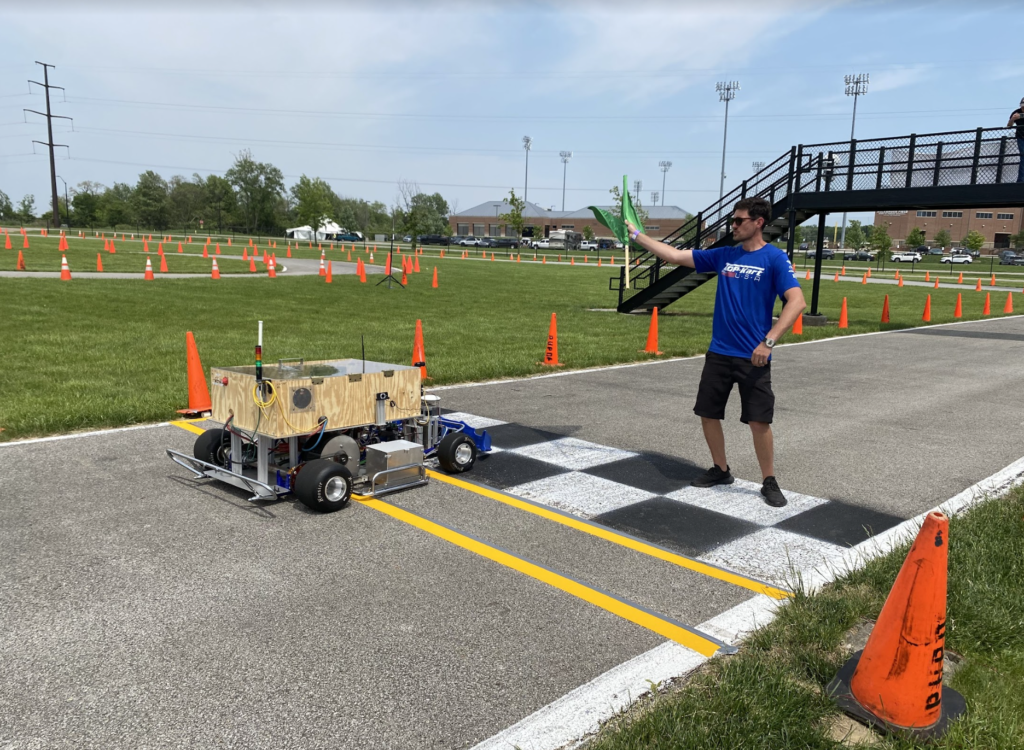
On race day on Friday, there were still some steering and braking issues. This led to the robot only going forwards and backwards, resulting in the fourth place finish.
Sam Walters, the former RoboRacing PM, said “Our main takeaway is that we were too ambitious with our goals and didn’t put in the hours appropriate to reach them in time.” The team will be spending the time until next competition doing minor improvements to aspects that were close to working, redesign aspects that didn’t make the performance cut, and trying to get the robot in a testable state for software much sooner in the year. Doing a complete redesign allowed for the team to do a lot of learning in such a short period of time, effectively having two competition seasons in a single year! The team is excited to put this vast knowledge gained to work on the next version of the robot!