by Jonathan Spalten
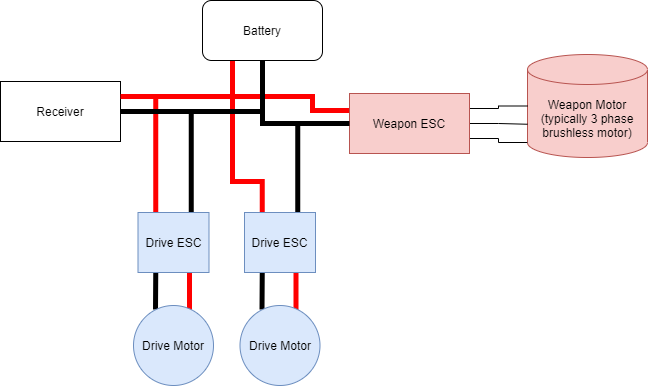
The main challenge of combat robots is designing and manufacturing a robust robot that can withstand the trials and tribulations of repeated contact with enemy robots and being flung around the combat arena, while budgeting weight to ensure they meet the weight limit imposed by their weight class. This challenge has to be kept in mind for every aspect of the combat robot. This includes the electrical system, the central system that enables the combat robot to work. To support this, combat robots usually have a simple, streamlined system of electronics. This electrical system is the focus of this article.
Most combat robots consist of two major subsystems: the drive train and the weapon system. These systems have two main components in common: the battery and the radio receiver. A typical combat robot utilizes a Lithium Polymer (LiPo) battery, notably used in a variety of applications that require a lightweight power source. LiPos have one of the highest energy densities of modern batteries, which makes them a logical choice for any application where weight is a concern. For smaller combat robots, it’s typical to use a single battery pack, but for larger robots, often two or more separate batteries provide power for the drive system and weapon system, often because the two operate at different voltages to better suit the higher speed motors used for weapon systems. Voltages are usually specified in terms of how many cells the LiPo battery has, with 3.7 V nominal per cell. A common voltage in many weight classes is 3s (11.1 V nominal), but some higher weight class robots can go up to 6 to 8s (22.2 and 29.6 V nominal) for their weapon systems to enable their weapon motors to go at high speeds and run at lower currents for the same amount of power.
The other major shared subsystem is the radio receiver. This takes in the signals sent from the remote controller that the operator uses and sends signals to the controllers within the robot that operate the weapon and drive systems. RoboJackets’ combat robots often use a simple 4 channel receiver as a tried and true controller that works for the vast majority of robots.
The next major components are the motors and motor controllers. These are what turn the signals that are sent from the receiver into motion. The motor controllers are often the major failure point of many combat robots, so great care is taken to ensure that they are well protected inside the robot, to prevent damage, as well as ensuring that their specifications are adequate to handle the voltage and amperage that robot robot motors need to run. This is where the types and typical specifications diverge wildly. Different robots have different needs for their motors, and the motor is what defines what the requirements are for a motor controller, often abbreviated to ESC, for electronic speed control. These requirements are mainly required voltage and current, but can have other requirements, such as whether the controller can run a motor in forward or reverse without changing the wiring. For most drive motors, RoboJackets and many other combat roboticists use brushed motors for the drive system because of their robustness and simplicity. They also typically have less demanding speed requirements than weapons. The speed requirements for weapons usually necessitate a brushless motor that is capable of higher speeds.
There are many specifications that go into a brushless motor that need to be considered and depend on the requirements for the weapon system. For example, a robot that spins a larger weapon, E.G. a shell spinner, will require a motor that can deliver higher torque to enable a faster spin-up, minimizing the time before they can damage the enemy. Additionally, they may not need as much rotational speed to deliver large forces because of the sheer mass of their weapon. A robot with a smaller weapon, such as a bar spinner, does not need as much torque to accelerate their weapon, but will want to achieve a higher speed to deliver as much force as possible. For drive motors, there are motor controllers that can control two motors in one board and handle the programming to turn the robot with simpler inputs. These boards are typically larger, but they are often used on 3 lb combat robots because of their simplicity.
This, however, is not the be-all-and-end-all of combat robot electronics. There are opportunities for RoboJackets to delve deeper into the electronics side of combat robotics. RoboJackets usually uses commercially available electronics from sources like HobbyKing and Scorpion Power Systems, but there have been discussions in RoboJackets about developing a RoboJackets motor controller that can better meet our specifications and build in other useful features, such as current control that could prevent accidental ESC burnouts, a common electrical failure. Additionally, last year the team developed a design for a “melty-brain” combat robot, Hocki, which constantly rotates and varies the speed between its two drive motors to make the robot translate in addition to rotate. It has some additional components that enable it to ascertain its rotational position and identify a given direction as “forward.” These represent new steps in delving deeper into the electrical systems of combat robots made by RoboJackets. In general, the system RoboJackets uses is simple and robust, and has room to grow and provide new useful functions that protect the components from electrical failures that can often cost a combat robot a win in a match.