by Joe Spall.
RoboJackets has participated in autonomous and RC Sumo competitions in California and Japan in the past as part of BattleBots. This semester RoboJackets has formed a separate team to compete in these competitions: RoboWrestling! For a quick recap, autonomous Sumo competitions involve two robots going head-to-head to localize and push their opponent off of the field. These robots typically have hundreds of pounds of effective weight due to the magnets on their underside pulling down towards the steel field. Additionally, robot reaction times need to be in the sub-second range to quickly defeat their speedy opponents. RoboWrestling has taken on new projects as a newly formed independent team while they prepare for the competitions in the coming year.
The team has entered their robots Kirbi and Gucci, which are on their second and third revisions, respectively, into prior autonomous Sumo competitions. In the beginning of RoboJacket’s autonomous sumo participation, the team was focused on creating a strong mechanical and electrical foundation for the software team to develop on. Now, our robots have matured to relatively stable platforms that are incrementally improved. Different design concepts can be tested on each bot individually, and the better-performing designs can be standardized between them. Some recent changes on these robots include increasing the TFMini Time of Flight (ToF) sensor density on the front by relocating the side sensors to the front. The ToF sensor uses lasers, similar to a LiDAR, to measure the time it takes to bounce off an object. This information can be used to estimate the location of an opponent. Since it is more likely for the robot to face their opponent directly, finer granularity of position estimation in that direction is desirable. With the greater density of sensors in the front of the robot, versus originally equal distribution across the front and sides, the robots can more accurately pinpoint their opponent’s location.
Each of the subteams have been working on projects on an individual basis. The electrical subteam has focused on testing new PCB designs for Gucciii and Kirbii. The board updates this year include the control, radio, and power distribution board. The new radio board allows for remotely configuring the robot and testing different strategies very quickly without the time-consuming process of uploading new code to the microcontroller. The other new board is the power distribution board, which takes over the previous partial job of the motor controller for powering the whole robot while also adding current sensing capabilities.
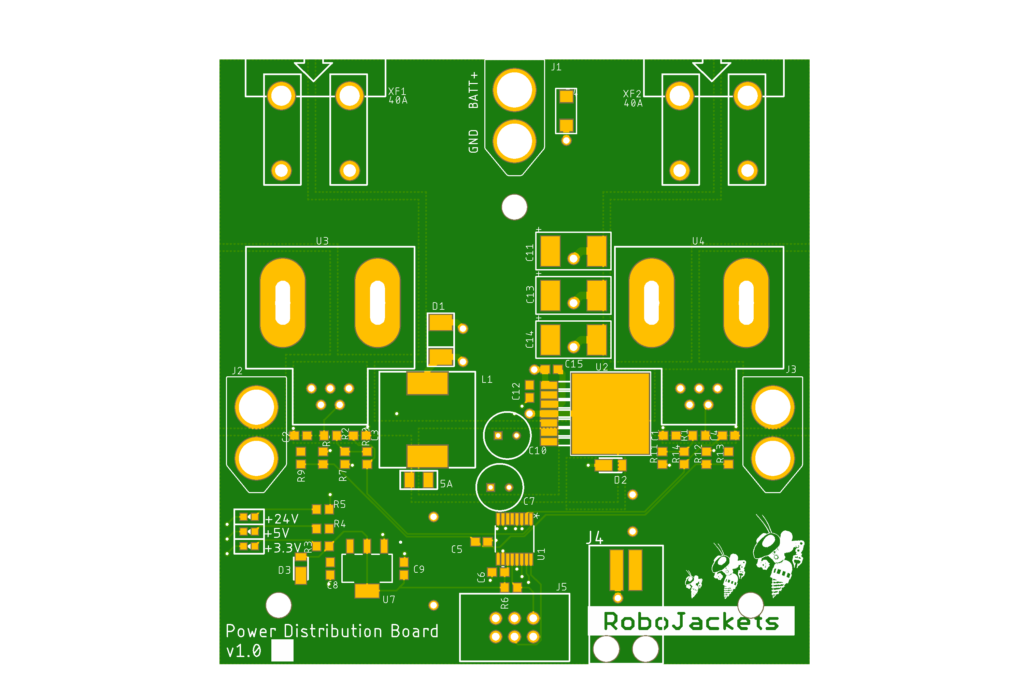
Software has been exploring new projects this semester as well. The primary focus has been developing a simulator to help quantify and visualize the robot dynamics. The primary focus is on collisions, which often make or break an autonomous Sumo competition round. The team is currently focusing on the visualization aspect, with a very early render of a match shown below. Additionally, the team has been working on developing firmware for the new radio board to incorporate remote configuration of strategies.
The mechanical subteam has also been making progress. They have been thinking through the designs of a brand-new robot, yet to be named. This has been helmed primarily by the new members on the team, allowing them to learn from the previous designs and bring in novel new ideas. One such new idea is a magnetized, hinged plow design. The plow, used to scrape the opponent off of the competition field, adds length to the robot which could be detrimental if the opponent were to get underneath the robot. A hinged plow significantly reduces the leverage gained by the opponent’s robot by hinging at the base to reduce the length of the lever arm created by the robot’s body. There are also magnets on the plow to keep it close to the steel field, reducing the likelihood of the opponent getting under our robot in the first place.
A great development from the formation of this new RoboJackets team has been the increase in interdisciplinary subteam projects. Electrical and mechanical have been working together to develop test beds for new sensors, along with generating motor speed and torque calculations seen below. Mechanical and software have been focused on modeling the robot dynamics in the simulator, generating the equations to accurately simulate collisions. Software and electrical have working on the firmware for the radio boards, helping to define necessary connections between the microcontroller and radio boards for communication. Overall, the team has grown and developed since becoming independent, and they are excited to see where the spring semester takes them.
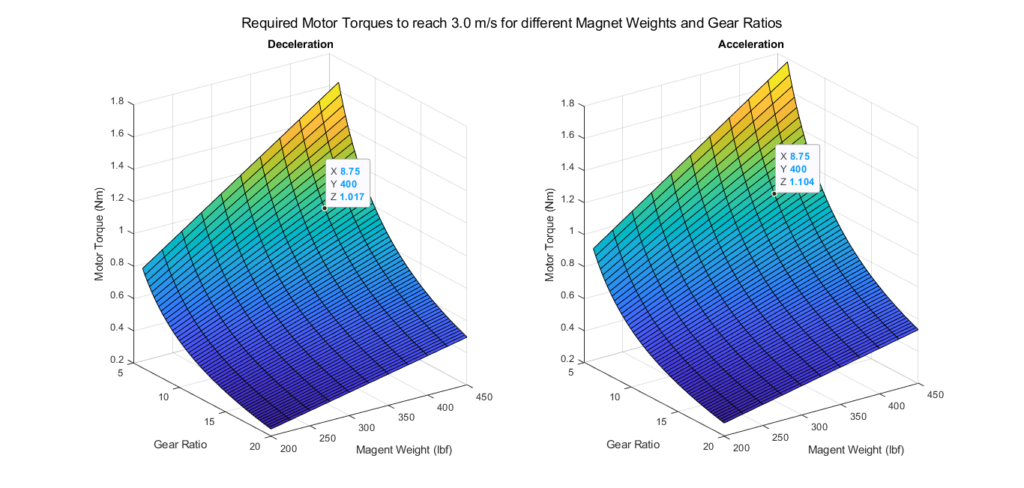
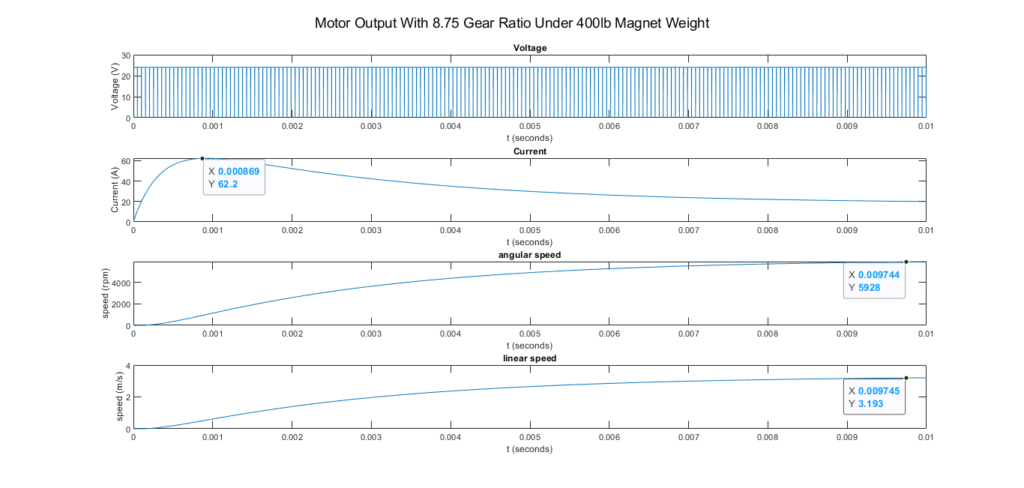