by Evan Bretl.
Despite the challenges brought on by the pandemic, RoboRacing has continued to move forward on its goals and invest in the future of the team. Both the Electric Vehicle Grand Prix (EVGP; normally held in April) and the International Autonomous Robot Racing Competition (IARRC; normally held in July) were canceled in 2020. Neither is canceled yet for 2021, but even if the 2021 competitions do not materialize, the team has substantial achievements to be proud of.
One unique opportunity that RoboRacing has stepped up to is working with the EVGP officials to help make close, wheel-to-wheel racing a more viable aspect of the event. Two topics in which we have lended our expertise are (1) planning for a standardized emergency stopping system and (2) making fast localization/tracking of opponent vehicles more achievable for all teams through standardized identifying markings. While this is a nice way to support the competitive robotics community, the primary goal for the year has been getting Rigatoni, our hopeful entry to EVGP, up and running.
For the hardware subteam, the top priority has been the major mechanical systems of Rigatoni. The vehicle started life as a race-ready electric go-kart (per competition rules) which we are retrofitting with actuated steering, brakes, and a fail-safe emergency brake. While it doesn’t have a ride-along seat like Bigolii did, Rigatoni is shaping up to be a showpiece for RoboJackets.
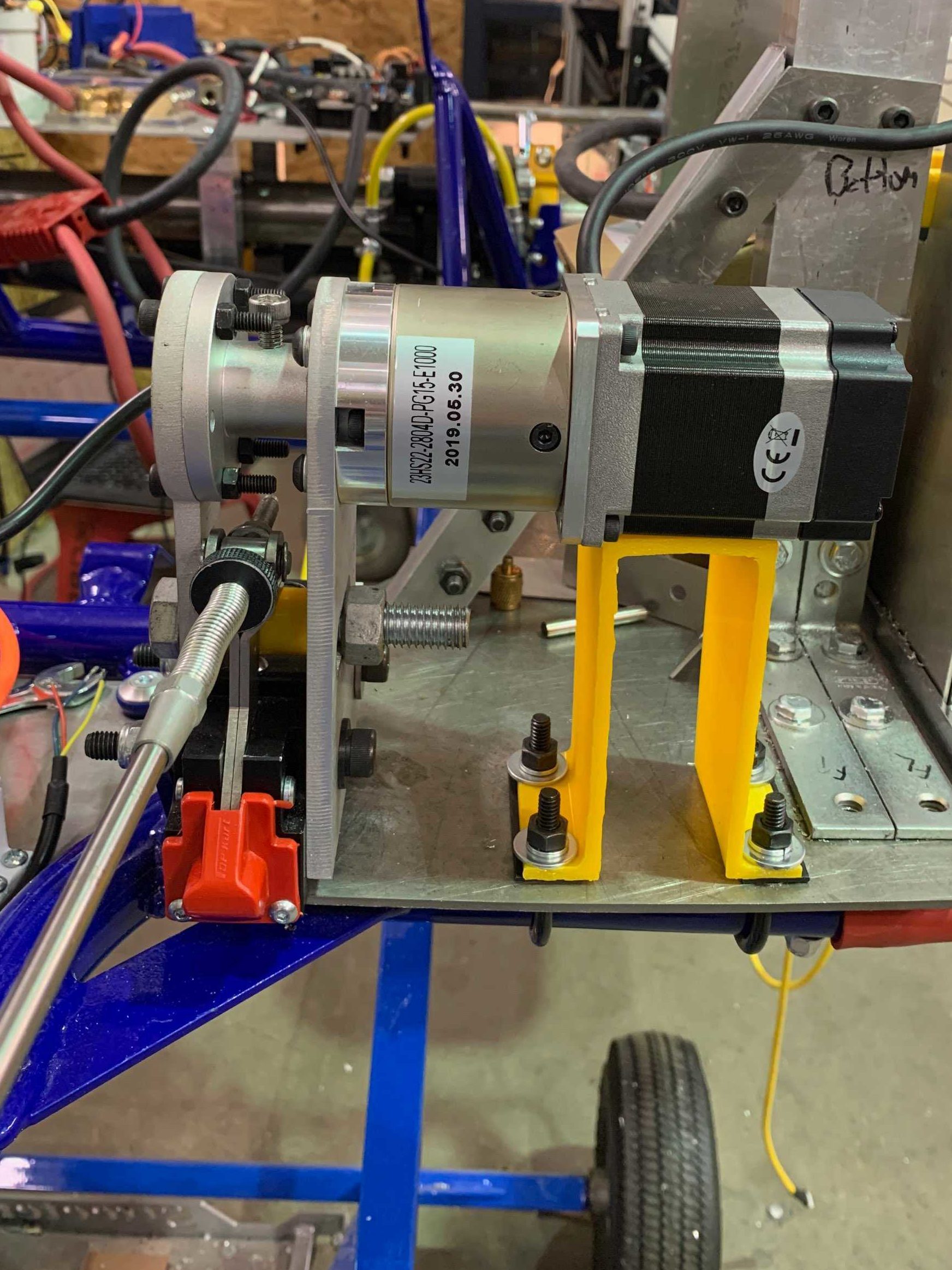
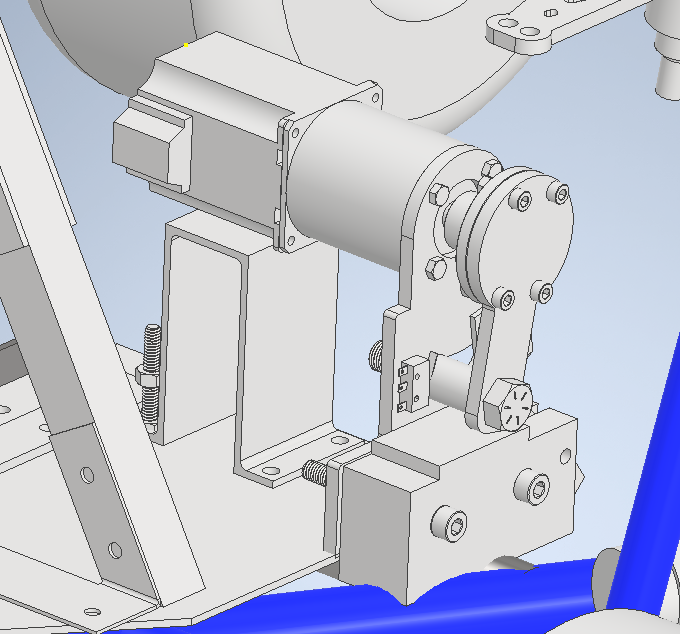
This year, RoboRacing has finished assembling all three of these critical subsystems. In particular, the hydraulic main brakes underwent a design iteration in 2020. According to Hardware Subteam Lead Sam Morstein, the braking system “uses a stepper motor to apply force to the [hydraulic] cylinder of the brake, so that the amount of braking force can be varied.” This is the first hydraulic braking system (and hopefully the most effective) in RoboRacing team history.
In conjunction with the mechanical subteam, the electrical subteam has also made substantial progress on implementing the major systems necessary to get Rigatoni driving. The wiring for Rigatoni was revised to improve safety. The system uses more separate PCBs for individual functions, so that a failure in one board does not necessarily bring down all functions of the vehicle. A new feature of Rigatoni’s electronics this year is power over Ethernet (PoE), and the PoE daughter boards have been assembled, verified, and revised this fall. Separate control boards operate stepper motor drivers for both the steering and main braking actuation. The emergency stop board has already been verified to work on-car, receiving signals from a remote and communicating with Rigatoni’s other systems.
New member projects on the electrical team also show a lot of promise. New member teams are working on making a custom axle encoder in-house to improve the way we measure Rigatoni’s speed and setting up multiple cameras to allow 360-degree vision around the vehicle. Another project involves a board which will allow external sensor modules to interface with the car’s existing systems. The first planned usage of this is a radar sensor facing backwards on Rigatoni to cover a blind spot when the vehicle is reversing or another vehicle is following. Between the mechanical and electrical subteam progress, the Rigatoni platform is approaching the day it can be tested with autonomy software in early 2021.
Of course, even the best robot platform isn’t much use without software to run it, and RoboRacing’s software subteam also showed concrete progress this year. It should be noted that in addition to the pandemic, the Software team also faced the additional challenge of having a large portion of its leadership graduate at the end of 2019.
The few returning members have been focused on making tweaks to the software stack to boost performance on the EVGP track. These improvements include both a global path planner and global path cost in the trajectory planner. The global path can be computed after the first lap around the EVGP track, allowing faster subsequent laps. Also, additional Gazebo (a 3D robot simulator) worlds were created to test the autonomy code with multiple opponents at the same time.
New members are generally working on improving Sedanii’s performance on the IARRC Urban Challenge. This challenge involves navigating a scaled-down grid of city streets by following signs to a destination. Notably, the team has iterated on our previous algorithm for detecting the presence and direction of the arrows which tell the vehicle to make turns.
Looking forward to 2021, the team is in a good position for EVGP and IARRC this year. Despite facing significant challenges, progress on Rigatoni hasn’t slowed, and we hope to bring you updates on testing soon!