by Jonathan Spalten.
Aside from the new member 2 lb program in Battlebots that we covered in our December issue, Battlebots subteams work on a variety of larger bots. This year our subteams of experienced members are working on combat robots in two weight classes: 12 lb hobbyweights and 30 lb featherweights. In this article, we’ll be sharing an update on the progress of each of these bots in the words of the subteam leads, and providing some pictures to show you what we’re working on. We also asked each subteam lead about what the biggest challenges they faced were. For any bot that’s a new iteration of an old bot, we also asked what the biggest changes were.
First, an update on Hocki, a “melty brain” hobbyweight whose entire body spins to hit its opponents with a single tooth instead of utilizing a separated drive and weapon system in more conventional combat robots. The relative speed of the two drive wheels is varied to control where the robot goes, requiring more advanced electronics and software. The team has made a lot of progress, including a complete CAD design, initial manufacturing of the chassis as well as some of the custom electronics required to operate the robot. Additionally, testing has been conducted to ensure the proper function of some of the control boards. The most recent work involves integrating the sensors on the control board in the software.
Varun Madabushi, bot lead for Hocki, highlighted a few challenges the Hocki team is working on, including manufacturing the outer ring of the robot. The ring was originally designed to be manufactured by wire-based electrical discharge machining (EDM), but because of issues in accessing on campus EDM machines, the manufacturing was outsourced to an external machine shop. On the electronics side, they have to balance complex systems with tight size requirements, especially on the design board which requires 4 subsystems. Additionally, to control the robot, the control software has to model the dynamics of the robot with limited data inputs from sensors. The team is planning to implement an extended Kalman filter, an industry standard nonlinear estimation strategy, to estimate the angle of the robot during its rotation.
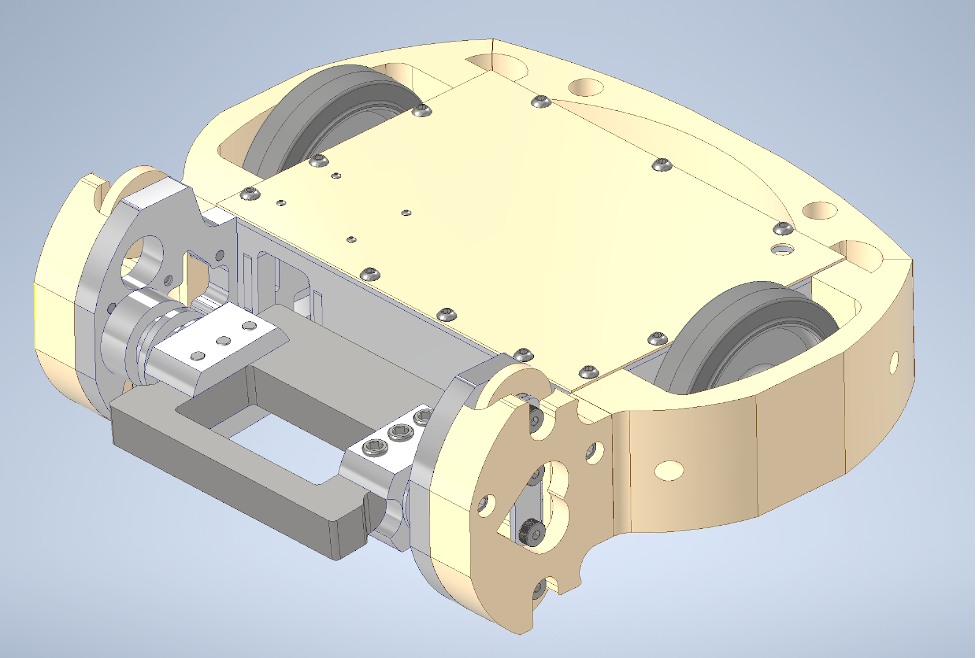
Next, we have an update on Maorii, the second version of a featherweight beater bar spinner. The team has made a great deal of progress this semester, and they have machined most of their chassis components. They plan to begin installing their electronics and drive system and machining their weapon at the beginning of next semester. Bot lead Dennis Crawford highlighted that the main challenge was determining the best way to manufacture the clamp that links their weapon pulley to the weapon itself. One success he highlighted was getting a significant number of their members trained on using the waterjet, enabling us to better utilize a very useful tool at our disposal. The main upgrades from the first version of Maori are an improved weapon electronic speed controller (ESC) to increase weapon spin up speed,an updated weapon design to lean further into the beater bar design, as well as a new armor design to better spread out the force of weapon impacts.
Next, an update on Samuraii, the second iteration of a featherweight vertical spinner with a hinged weapon mount to ensure the weapon hits consistently even when the robot is inverted. The progress the team made this semester was finalizing their CAD design and machining some essential components including major chassis plates and turning pulleys. Dylan Adriano, Samuraii Lead, highlighted the limitations on manufacturing time imposed by COVID restrictions as the biggest challenge the Samuraii team faced. The team had to work to design the robot to be easily manufactured and had to focus on planning shop time to efficiently get their manufacturing done. He highlighted the fact that they were able to overcome these challenges and still make progress through careful planning, a big success for the team. In line with these manufacturing challenges, the team focused on design for manufacture and assembly in this iteration of Samuraii, including a simplified rectangular chassis and reducing the required number of bolts for assembly. Additionally, the team added another set of wheels to improve mobility, and reinforced the chassis to improve robustness.
Our penultimate robot update is Valkyrii, the second iteration of a featherweight “undercutter” style horizontal spinner. The team made a lot of progress over the summer reworking the weapon and chassis design, and hit the ground running on machining bot components in the fall semester. They’ve made significant progress in machining chassis plates. They also are reusing the pulley from Valkyri, which will save them valuable machining time. Sam Li, Valkyrii lead, said the biggest challenge in the design process was managing the weight of the robot. At first, they were as high as 10% overweight, but they were able to modify the parts to get the robot to meet their weight requirements while balancing manufacturability. This new version of Valkyrii is designed to utilize modular weapons that can be used interchangeably to better respond to challenges imposed by an opponent. They have two different weapon designs: a disc type weapon and a bar type weapon. The disc has a high moment of inertia, and therefore hits hard to take down tough opponents. The bar has a lower moment of inertia, enabling a faster spin up time, but weaker hits. This is to counter faster robots that rely on ramming attacks, like our eternal enemy, wedges. Additionally, they changed their armor to include nylon fibers to increase strength and a curve to cause enemy blows to glance off. They also made upgrades to the electronics system to include programmable ESCs and censored motors for the drive system to improve drive control.
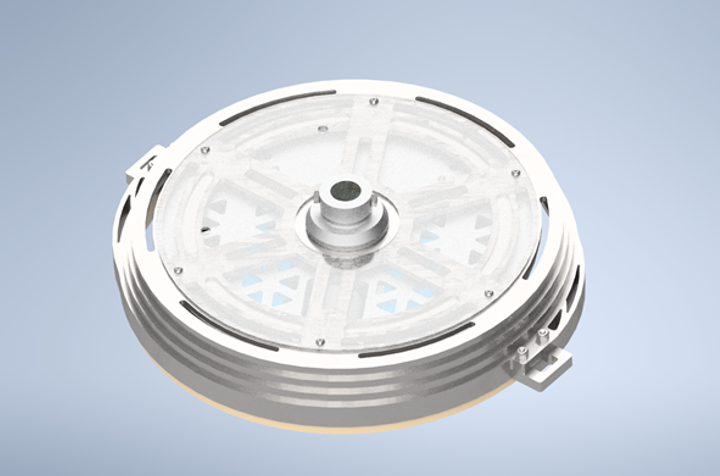
The final robot update this year is Chonki, a hobbyweight shell spinner with a shuffling drive train. The team has made major progress, including an almost-completed chassis assembly. The remaining work is the construction of the shuffler system and weapon manufacturing. Brian Epstein, Chonki lead, said that the main challenge for Chonki was manufacturing the outer ring. The team considered a few different designs, starting with a concept that involved bolting or welding several water jetted layers to create the stepped ring shell. The team made heavy use of FEA to evaluate their designs iterations, eventually settling on taking a single piece of steel that will be CNC milled to the specified shape. This new design presents a major challenge in handling and fixturing a 250 lb block of steel in our CNC mill.
This semester has been a productive one for Battlebots’ experienced member teams, with a variety of challenging robot designs and restrictions imposed on manufacturing. Despite these, the teams have persevered, and each team has made significant progress in manufacturing their robots. The progress they’ve made this semester will ensure the teams are set up for continued success in the spring semester.